Dynamic, precise and fast measurement of the H2 concentration is essential for the operation of a mixing system for enriching the natural gas pipeline with hydrogen from 0 to 100 per cent by volume. The gas analysers from Archigas meet the special challenges by means of a further developed form of thermal conductivity measurement.
Specific advantages
- High precision and speed: with very high accuracy of less than 100 ppm for H2 in CH4 mixtures and response times down to 30 ms predestined for the application area
- Robustness and longevity: resistant to moisture in the background gas and suitable for long-term use of up to 10 years
- Cost-effectiveness: no complex sample preparation required – therefore cost-efficient and easy integration into existing systems
- Adaptability: designed for easy installation in the mixing node or directly in the line
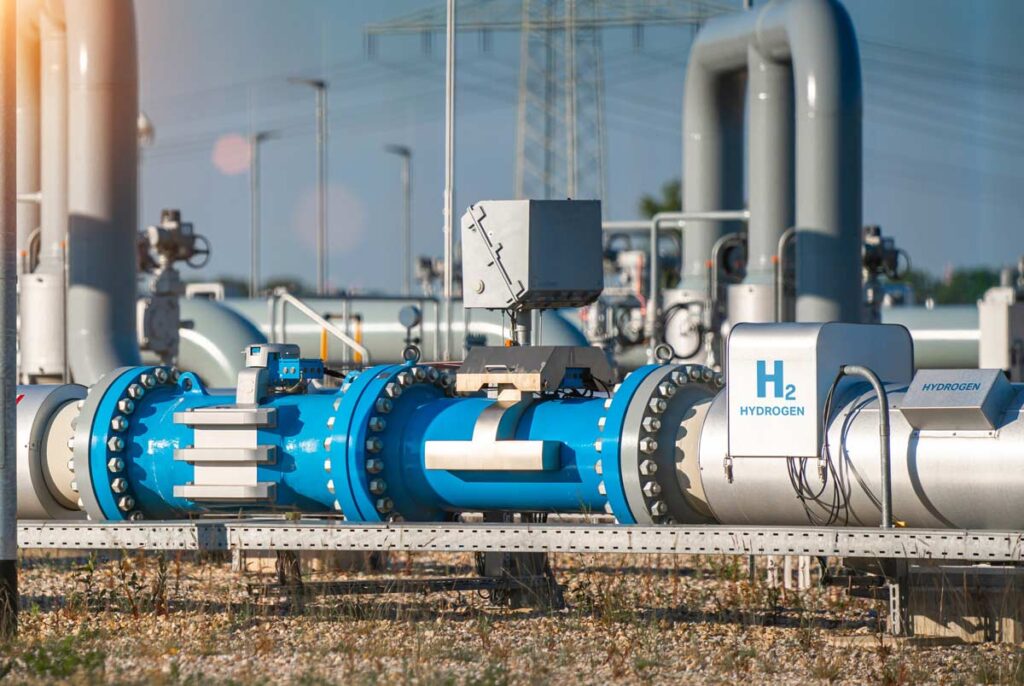
Reasons for blending H2 into natural gas
- Reduction of CO2 emissions: Adding hydrogen to natural gas reduces the carbon content of the fuel, which leads to lower CO2 emissions during combustion. This is an important step towards reducing greenhouse gases and achieving climate targets
- Integration of renewable energies: Hydrogen can be produced from surplus electricity from renewable energy sources such as wind and solar power. By blending hydrogen into natural gas grids, this renewable hydrogen can be efficiently utilised and stored
- Increasing energy efficiency: Hydrogen has a higher energy content per kilogramme than natural gas. Blending can increase the calorific value of the gas, leading to more efficient energy use
- Long-term infrastructure transformation: blending hydrogen into existing natural gas networks enables a gradual transition to a hydrogen economy without the need to build a completely new infrastructure immediately. This facilitates the transition to a more sustainable energy supply
- Industrial applications: In certain industrial processes, blending hydrogen with natural gas can improve efficiency and performance. For example, the calorific value and combustion temperature can be increased in high-temperature processes
- Technological development: The addition of hydrogen to natural gas makes it possible to test and further develop technologies and infrastructures that will be needed for the future hydrogen economy. This includes the development of sensors, safety systems and regulations for the safe and efficient handling of hydrogen-natural gas mixtures
Challenges of H2 measurement in natural gas
- Moisture and particles in natural gas can damage conventional sensors
- Unknown composition of the natural gas leads to cross-influences when measuring using thermal conductivity
- Safety requirements demand that samples are not released into the environment
- High pressures can destroy measuring devices
Mastered by Archigas H2 gas analysers
- Sensors are resistant to high humidity and particles
- Precise calibration minimises cross influences due to unknown compositions ensures high accuracy
- The sample remains safely in the system and does not escape into the environment
- High reliability and durability are guaranteed by pressure resistance up to 200 bar
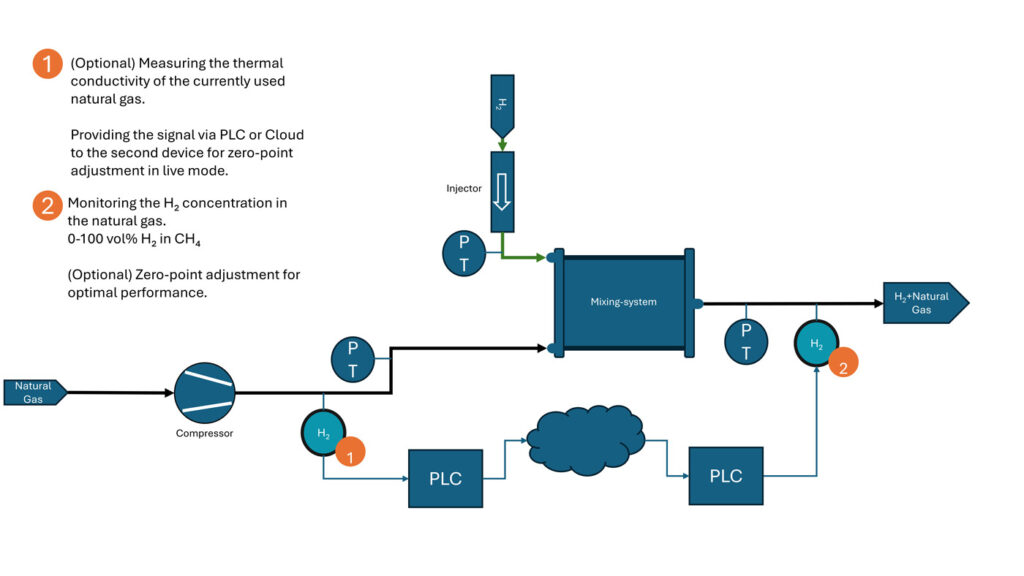
How to measure
Measuring the hydrogen concentration in natural gas using thermal conductivity
Measuring the hydrogen concentration using thermal conductivity is an established method that has been known for over 100 years. This technique offers high precision and reliability in determining the H2 concentration in gas mixtures. Further information can be found in the FAQs.
Logic behind the measurement: The thermal conductivity measurement is based on the fact that hydrogen (H2) and methane (CH4) have different thermal conductivities. In a binary gas mixture such as H2 in CH4, methane acts as a background gas. The resulting measurement signal is linear and enables a very precise determination of the H2 concentration.
Measurement in multi-component gas mixtures: If the background gas consists of several components, such as air, and the concentrations of these components remain constant, this gas mixture can be set as the background gas. In this case, the measurement of the H2 concentration remains accurate.
Challenges with fluctuating gas mixtures: Problems arise when the concentration of the individual components in the background gas fluctuates, as is the case with natural gas. Fluctuations in the CO and CO2 concentrations lead to deviations in the measurement signal, as the zero point of the measurement is shifted.
Solution: Dynamic zero point adjustment: To overcome this challenge, natural gas can be measured without the addition of hydrogen. This value serves as the zero point and is passed on to all other devices. As a result, the zero line is always dynamically adjusted to the corresponding natural gas mixture and the measurement remains flexible and precise.
A typical measurement setup could look like this
- Measurement without H2 admixture: Natural gas is measured without hydrogen to determine the zero point.
- Measurement with H2 admixture: The H2 concentration in the mixed gas is measured taking into account the dynamically adjusted zero point.
This approach ensures that the measurement of the hydrogen concentration in the natural gas remains reliable and accurate even with fluctuating background gases. The TCD3000 SiA gas analysers from Archigas offer the optimum solution for this.
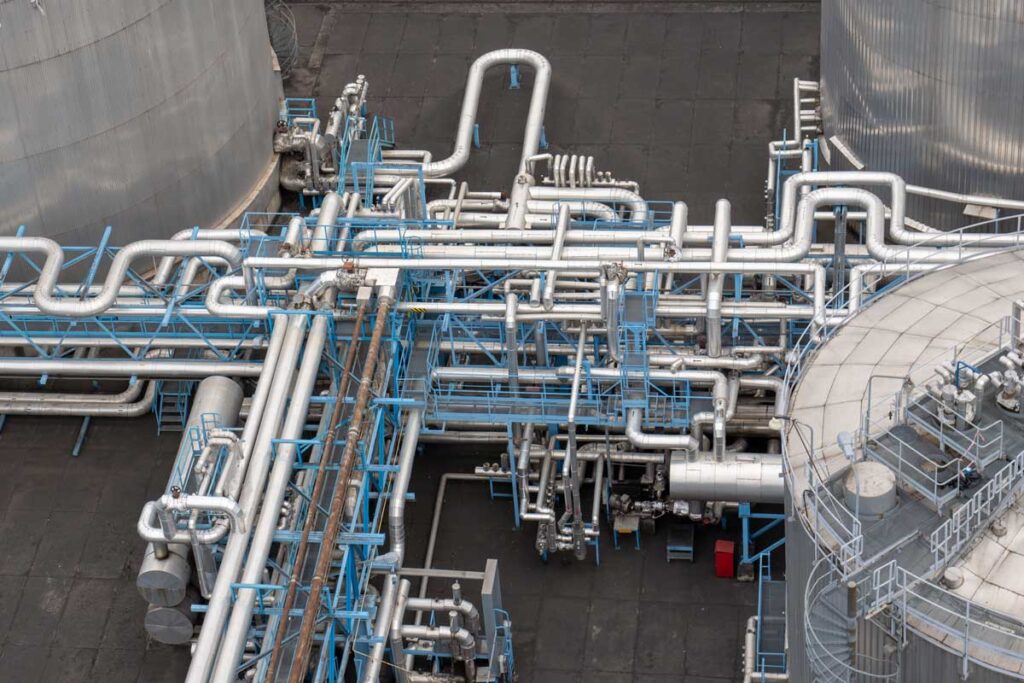
Discover other areas of application for Archigas gas analysers
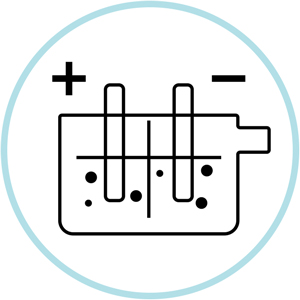
Electrolysis
Monitoring of UEL / LEL and purity, e.g. for H2 electrolysis
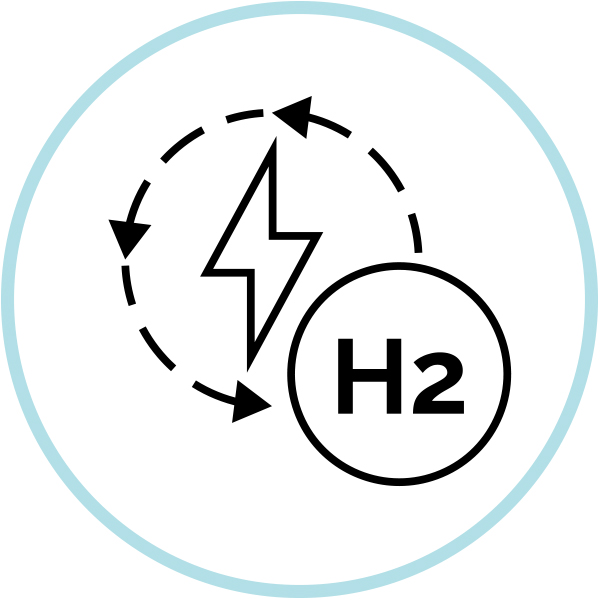
Fuel cell
Monitoring the hydrogen concentration in the exhaust gas train
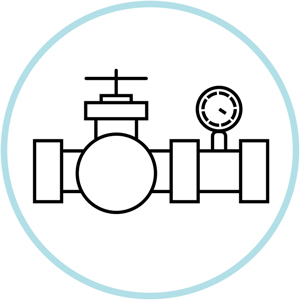
H2 in natural gas
Determination of the hydrogen content in natural gas networks up to 100%
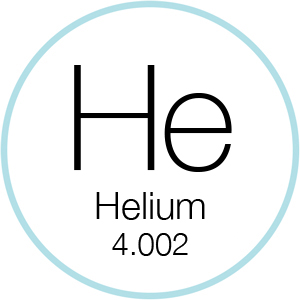
Helium measurement
Fast and precise helium detection without detours
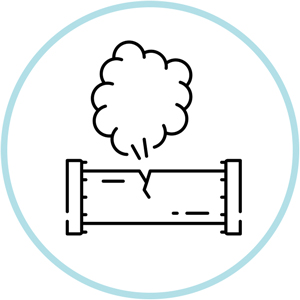
Leak testing
Automated detection of leaks for monitoring
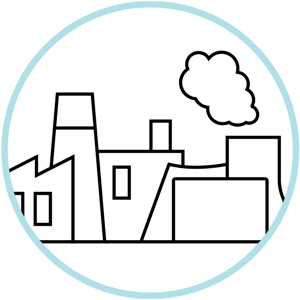
Further areas of application
Purity control, purge gas monitoring, measurement of other binary or quasi-binary gas mixtures