General Information
A gas analyzer measures the concentration of specific gases in a gas mixture sample. Archigas gas analyzers use thermal conductivity detectors (TCDs) to determine the concentration of binary and quasi-binary gases. |
|
A thermal conductivity detector (TCD) measures the change in the thermal conductivity of a gas mixture. Each gas has a specific conductivity. By changing from one conductivity to another, the concentration of one gas in another can be determined. |
![]() |
![]() |
1. Archigas TCD3000 WLD
Advantages:
- Very high reaction speed (30 ms)
- High long-term stability
- Low maintenance requirements
- Robust against moisture in the process gas
- No position dependency
- Very large, dynamic measuring range from a few ppm to 100 vol.%
- Use at high pressure
- Very low flow dependency
- Less sample preparation
- High detection limit
Disadvantages:
- No selectivity
- Pressure dependence (but can be compensated)
2. Other WLD
Advantages:
- High long-term stability
- Low maintenance requirements
- Dynamic measurement possible
- Linear measurement behavior
Disadvantages:
- Often flow-dependent
- Sample preparation required
- Pressure-dependent (but can be compensated)
- Average reaction speed (1 s – 120 s)
- Not robust against moisture in the process gas
3. Catalytic (pellistor)
Advantages:
- Low price
- Sensitive to sample gas
- Higher selectivity
Disadvantages:
- Only small measuring ranges
- Non-linear measuring behavior
- Low reaction speed (10-80 s)
- Irreversible damage due to contact with e.g. halogens or combustion reactions without oxygen
- High maintenance requirements
- Not robust against moisture
4. Semiconductor
Advantages:
- Low price
- Good detection limit
- Low maintenance requirements
- High sensitivity
- Very good selectivity
Disadvantages:
- No concentration measurement possible
- Average reaction times
5. Electrochemical
Advantages:
- Very low price
- Low energy consumption (< 2 W)
- High sensitivity
- High selectivity
Disadvantages:
- Slow reaction speed
- Low long-term stability
- High maintenance requirements
- Not robust against moisture in the process gas
- Position dependent
The gas analyzers are designed for the measurement of binary and quasi-binary gas mixtures (e.g. H2 in air, CH4 in CO2 etc.)
A gas mixture consisting of two gases: measuring gas and background gas
A quasi-binary gas mixture consists of more than two gases (e.g. air) – whereby the background gas mixture consists of several gases that are present in stable, low concentrations or have similar thermal conductivities.
Cross sensitivity describes the undesirable reaction of a sensor to gases or other influences such as pressure or temperature that are not the target of the measurement. This distorts the measurement result and affects the accuracy of the measurement. Cross sensitivity represents a challenge in the accurate measurement of gas concentrations. By carefully selecting and applying measurement technologies and using suitable calibration and compensation methods, the effect of cross sensitivity can be reduced in order to achieve more reliable and accurate measurement results.
Target gas: hydrogen (H2) Background gas: oxygen (O2) Third gas: nitrogen (N2) Unknown parameters: concentration, pressure and humidity
Explanation: This binary gas mixture consists of the target gas hydrogen (H2) and the background gas oxygen (O2). It is assumed that this mixture will be used in various applications such as fuel cells or electrolysis processes.
Problem of cross sensitivity: If nitrogen (N2) is also present in this binary mixture in an unknown concentration, this can affect the measurement. The cross-sensitivity of the sensor to nitrogen could lead to the displayed concentration of hydrogen being distorted and displayed as a negative value. The reason for this is the lower thermal conductivity of nitrogen compared to oxygen.
Other unknowns: The pressure of the gas mixture and the humidity are unknown, which further complicates the measurement. Both pressure and humidity can affect the accuracy of the measurement.
Minimization strategies
- Calibration of the sensor: If the nitrogen content in the gas mixture is constant, regular calibration of the sensor with a known gas mixture containing nitrogen can minimize the effects of cross-sensitivity.
- Adjusting the measuring range: If nitrogen is introduced as part of the process, the device can be calibrated so that 4 mA corresponds to pure nitrogen and 20 mA, for example, 4 vol.% H2 in O2. In this way, H2 in O2 and O2 in N2 can be determined with one device.
- Compensation algorithms: If one of the interference components is known from other measuring instruments, the influence of this component on the measurement result can be corrected using mathematical algorithms. Thermal conductivity is very suitable for calculation because the cross-influences are reliably reproducible.
The pressure of a gas mixture influences the measurement of thermal conductivity. This pressure influence depends on the type of gas. For gases with lower thermal conductivities such as oxygen, the dependency is lower. For gases with high thermal conductivity such as hydrogen, the dependency is higher. This influence is greatest at low pressure, especially in the range of 1 to 2 bar.
As the pressure increases, the density of the gas increases, resulting in a more stable thermal conductivity. From a pressure of around 7 bar, the influence of pressure on the thermal conductivity measurement is less and becomes smaller and more linear as the pressure increases. This means that at high pressure, the measurements are more accurate and less susceptible to fluctuations.
By using compensation algorithms, available on request for Archigas devices, this influence can be effectively eliminated, enabling precise measurements even under variable pressure conditions.
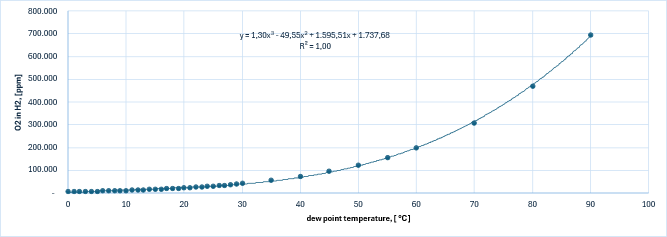
Technical specifications
The precision of the gas analyzers is less than 1% of the measuring range.
Basically, the flow dependence is very low and lies below 1000 ppm.
The optimal flow rate for the TCD3000 transmitter is between 30 and 120 liters per hour.
The screw-in versions TCD3000 Si and SiA can measure at flow rates of up to 10 m/s.
The gas temperature should not exceed 90 °C. Thermostabilization can be adjusted up to 130 °C, which means that the gas temperature can be up to 120 °C.
Installation requirements
- Gas analyzer transmitter: 6 mm tube.
- Gas analyzers Si and SiA: G1/2″ & NPT1/2″
The gas analyzer transmitter is designed for screw mounting. The pneumatic connection is made via a G1/2″ or NPT external thread with O-ring. A metal-to-metal seal is also available on request. After completing the installation, the technical tightness should be checked.
The ATEX variant is the TCD3000 SiA with the following specifications:
ATEX ZONE 1 II 2 G Ex db IIC T3 Gb (-40°C < Ta < +90°C)
On request also:
ATEX ZONE 1 II 2 G Ex db IIC T4 Gb (-40°C < Ta < +120°C)
The TCD3000 transmitter variant can be connected as a bypass.
werden.
The TCD3000 Si or SiA screw-in versions can be implemented directly into the process with high pressure and flow
.
The voltage can be between 18 -30 VDC
(other power supply options on request).
Communication
- Analog signal 4-20 mA (NAMUR 43)
- Digital interface RS485 (ASCII)
The calibration procedure is carried out by sending the appropriate commands via the RS485 interface:
• Single-point calibration: send the command AO (address + ‘O’)
• Two-point calibration: send the command AS (address + ‘S’) twice, once at the beginning and once at the end of the measuring range.
Calibration and Maintenance
Calibration is carried out by passing pure measuring or background gas through the device. The calibration process is triggered via digital communication (RS485). One-point and two-point calibration are possible.
One-point calibration:
This type of calibration involves shifting the entire measuring span to the zero point. In most cases, a one-point calibration is sufficient. This method is recommended when commissioning.
Two-point calibration: During the two-point calibration, the measuring span is adjusted.
Calibration should only be performed when the signal is stable. After each calibration process, the device sends back the current data set with the measured value.
The following applies to the frequency of calibration:
- The test interval depends on the measuring range. The smaller the measuring range, the more often the device should be calibrated
- In 90% of cases, a one-point calibration every 6 months is sufficient
- It is recommended to carry out a reference measurement in order to adjust the calibration intervals
Applications
In principle, the gas analyzers can be used in humid environments up to 100% (liquid water). However, during installation, it should be ensured that the liquid does not block the gas access to the sensor.
Offers & Support
In order to receive the best possible product offer, it is advisable to specify the following aspects when making an inquiry:
- Area of application
- Measuring and background gas
- Gases in the mixture
- Humidity and dew point
- Required accuracy
- Flow rate
- Process pressure
- Gas temperature
- Ambient temperature range